Share This Article
One cannot deny that the earth’s population is growing, and with it, so is the need for infrastructure. As we search for more and more spaces to accommodate the rising population, it is also imperative to be mindful of the carbon footprint each building leaves on earth and the manmade emissions caused by construction. Today many advancements have been made in the industry to reduce energy consumption and lessen the harmful impact on Earth. One of the popular solutions to this is modular construction and prefabrication.
What is Modular Construction and Prefabrication?
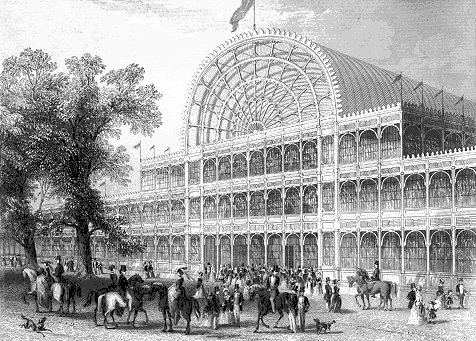
Modular Construction is an off-site construction in which materials are built elsewhere and assembled on-site. The materials are fabricated in the factory, under controlled conditions. Most buildings are almost completed offsite and these modules are transported to the site for final assembly.
Prefabrication in construction, as the name suggests, refers to materials that are ?pre-built? and manufactured offsite, which are transported to the site for assembly. Modular Construction and prefabrication are almost similar except for one thing. Modular construction aims to standardise the design process by using modular forms called modules. Both prefabrication and modular construction follow appropriate building codes and regulations.
How can urban areas benefit from modular construction?
- It saves time: One of the major advantages of prefabricated building systems is its reduced timeline and increased speed of construction. The materials are manufactured elsewhere, delivered quickly and assembled on-site.
- It saves money: Modular construction saves time and hence money. Skilled labour is also expensive and in short supply in most cities. Off-site construction methods cut labour costs by a significant margin and even reduce the overall cost by up to 25%.
- Eco-friendly: every construction leads to some waste. Modular construction uses energy-efficient and eco-friendly materials that can be reused easily leading to much less wastage compared to traditional constructions, which can be hard to get rid of and highly undesirable in congested urban settings.
- Less chance of delay: Prefabrication ensures that less delay occurs during construction. The delay in construction due to weather conditions is low as materials are manufactured in conditions unaffected by the weather. Materials do not have to be frequently delivered, resulting in less delay due to traffic congestion.
- No need to store materials: One of the major concerns of constructing in an urban area is space to store materials. When a site is small, the dilemma of storing materials can slow down work and even lead to theft. In this situation, prefabrication arrives as the ideal solution.
Best practices for modular building designs


- Modular manufacturers play a crucial role in modular construction projects, providing consultation and design-assist services. They are experienced in the complexities of modular construction and can help address efficiencies and risks during the design phase.
- Consulting the manufacturer early can maximize flexibility in design options, ensure design specifications do not require materials or products that may extend the schedule, promote value engineering, control and reduce transportation costs, construction costs, ensure constructability, design for efficiency and reduced waste, and minimize risk throughout the process.
- Architects should establish the specific scope of the manufacturer’s responsibility related to these services and ensure they are approved in the state where the project will be located. The success of a modular construction approach depends on clear communication and coordination between the design team, modular manufacturer, and on-site construction management team.
- Building Information Management (BIM) tools like Revit can improve the design, manufacture, and assembly process by ensuring construction tolerances, preventing conflicts, and providing flexibility through robust virtual prototyping. However, strict BIM standards are essential to avoid errors.
- Modular-based design should consider the fabrication, transportation, and connection of components, allowing for a more iterative and less linear process. Initial design considerations should be guided by geometric design, transportation constraints, and the building’s division into modules.
- Collaboration with the modular manufacturer and construction manager is crucial for developing detailed connections and optimizing the manufacturing process.
Prefabricated vs traditional construction: Which is better?
- Strength and Durability: Compared to traditional buildings, prefabricated constructions are more structurally robust and have better finishing. Before being constructed on site, the materials are tested and pre-cut. This guarantees that every component fits together precisely and is resistant to adverse weather. Because prefabrication provides more control over the materials and components utilized in the production process, it can result in superior quality and longevity.
- Sustainability: Modular construction methods are sustainable since less energy is needed to manufacture and transport materials. Prefabricated buildings may also be designed with double-glazed windows, insulation, and other energy-saving measures, making them extremely energy-efficient.
- Design: Traditional construction is extremely adaptable to design because it is constructed on-site. Since the materials are prefabricated in modular construction, it has limitations on the design. However, modular construction can look clean and modern, which is desirable for those with contemporary tastes.
- Construction speed and cost: Prefabricated building systems reduced construction timeline. Traditional construction takes more time as it is built on-site by workers who have to figure out how to build it, as they go. Traditional construction is also costlier due to the same reason.
Smart technologies in modern modular homes

Smart building technology is transforming the way we live in modern housing, offering innovative solutions that enhance the quality of living in a cost-effective and environmentally friendly manner. This trend includes incorporating smart systems in modular homes, which provide numerous benefits such as customization, energy efficiency, and improved comfort. Smart home automation options in modular homes include smart locks, lighting systems that adjust based on natural light levels, remote thermostats, and home security systems that provide real-time alerts and surveillance.
Smart thermostats can reduce heating and cooling costs by adapting to schedules and preferences while lighting systems adjust based on occupancy and natural light. Energy monitoring systems provide insights into energy consumption, aligning with the growing global emphasis on sustainability and responsible living.
Smart security systems in modular homes offer features like remote monitoring, motion detectors, and automated alerts, keeping homeowners informed and in control. Smart locks and safety features like smoke detectors and carbon monoxide sensors ensure a higher level of safety. As technology continues to evolve, smart technology in modular homes will continue to revolutionize the concept of home.
Modular construction may be hard to crack right now, but with time, it can replace traditional construction completely, resulting in smarter and more sustainable homes.
Sources
- https://www.ucem.ac.uk/whats-happening/articles/what-is-prefabrication/#:~:text=Prefabrication%20can%20be%20faster%20than,faster%20than%20their%20traditional%20equivalents.
- https://www.realprojectives.com/the-advantages-and-challenges-of-modular-construction/
- https://www.iccsafe.org/building-safety-journal/bsj-dives/the-benefits-of-modular-construction-in-urban-settings
- https://plusspec.com/modular-construction-tips-tricks-for-designing-a-modular-building/
- https://www.vrisainnovation.com/blog-details/7/prefabricated-construction-vs-traditional-construction#:~:text=Prefabricated%20buildings%20also%20use%20fewer,can%20save%20time%20and%20money.
- https://www.360connect.com/product-blog/prefabricated-vs-traditional-construction
- https://www.tinyhouse-company.co.uk/blog/smart-home-in-a-modular-house-which-technologies-are-worthwhile
- https://greenvalleyhomesales.com/the-smart-home-revolution-integrating-technology-in-modular-homes/